zurück zum Blog
Schlüsselkomponenten im Prüfstandsbau
Wenn wir uns Gedanken über neue Prüfmethoden machen oder für Kunden Prüfanordnungen entwickeln, dann geschieht das in 99% der Fälle in einer bewährten Pipeline, von der Reibstelle ausgehend:
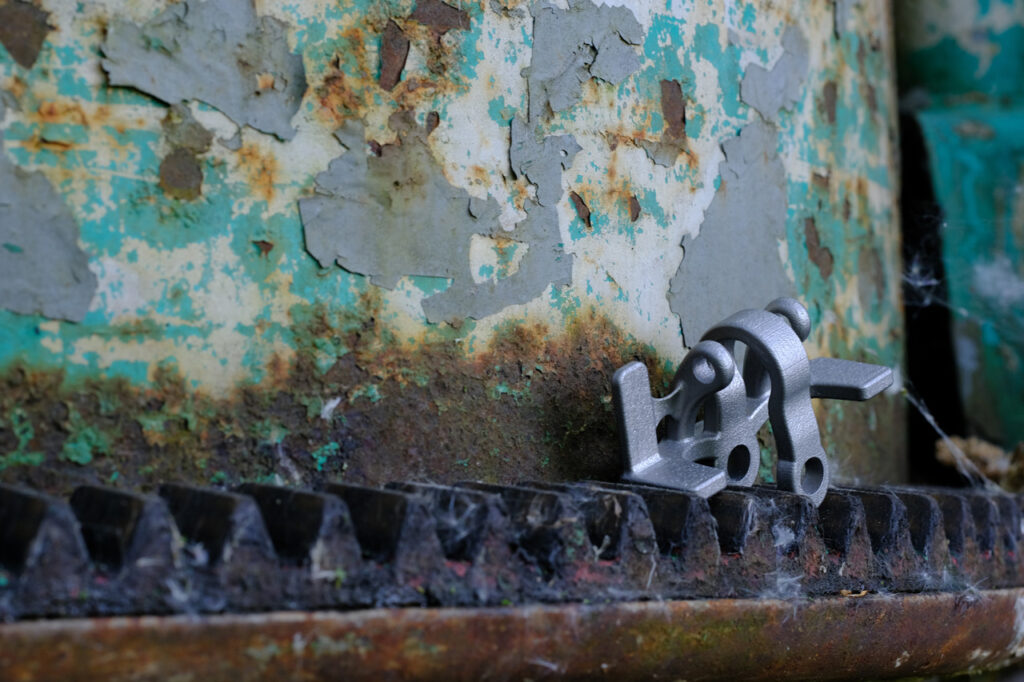
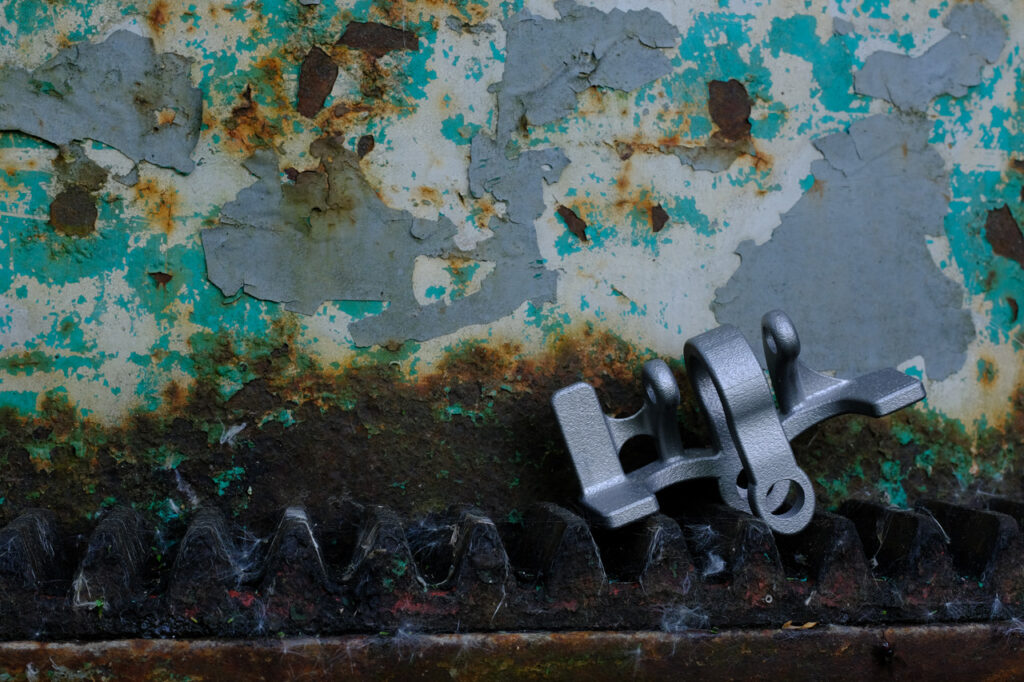

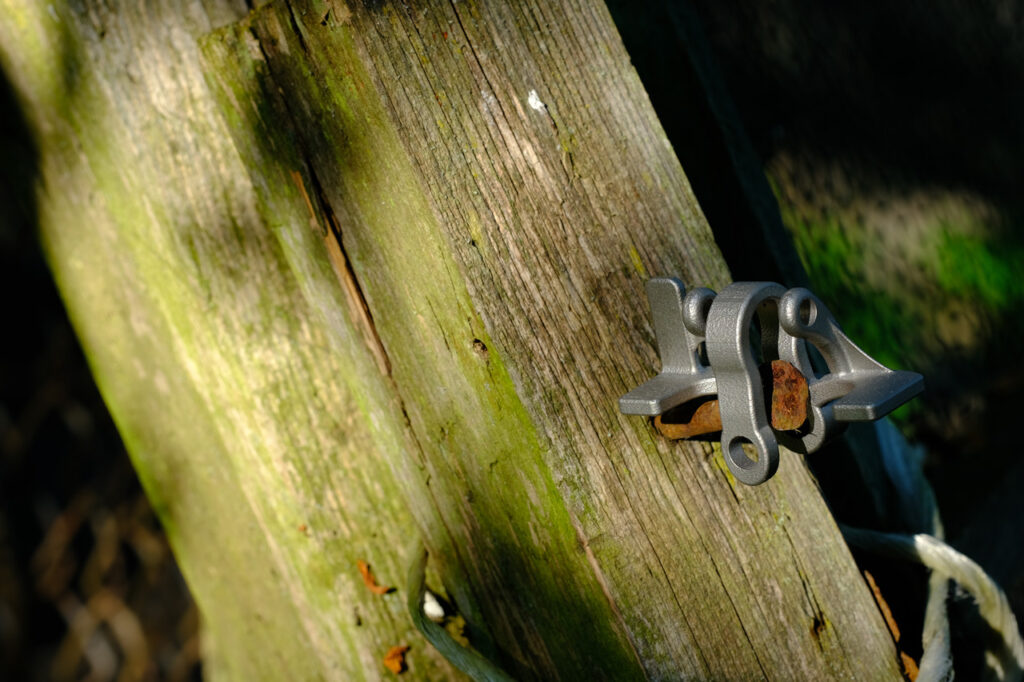
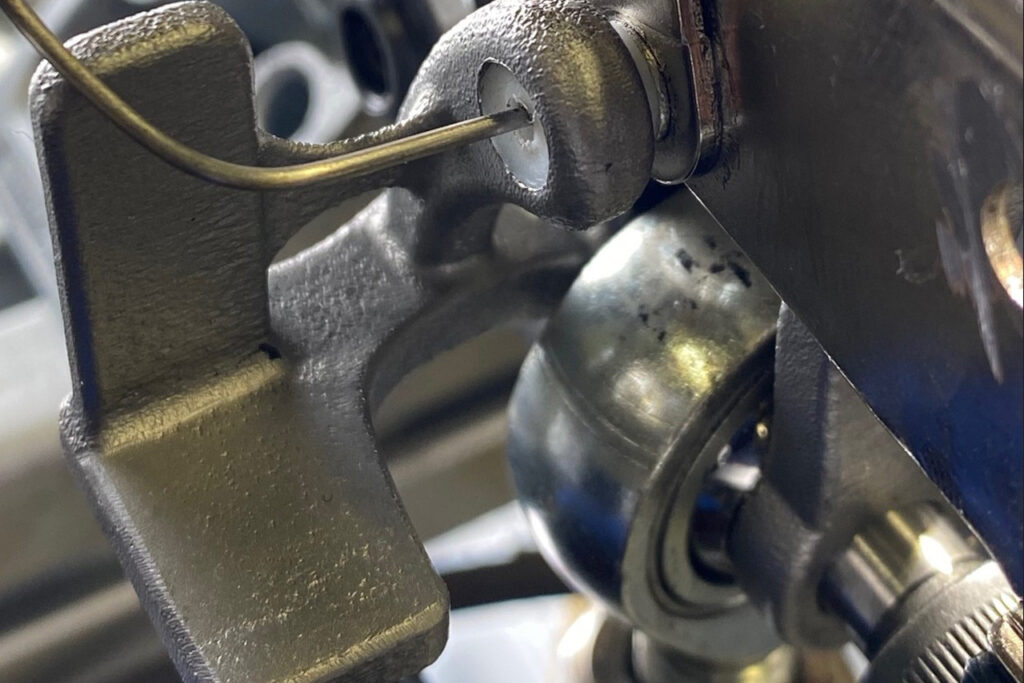
Wenn wir uns Gedanken über neue Prüfmethoden machen oder für Kunden Prüfanordnungen entwickeln, dann geschieht das in 99% der Fälle in einer bewährten Pipeline, von der Reibstelle ausgehend:
Erst überlegt man, welche Geometrien im Realsystem im Kontakt sind, welche Relativbewegungen diese zueinander ausüben, ob es überlagernde Aktorik gibt, welche Medien die Oberflächen trennen könnten und wo fest und lose im System ist. Man untersucht, welche Bewegungs- und Beschleunigungsformen im Realsystem anzutreffen sind und wo die Grenzen des Belastungskollektivs sind.
Ist man hiermit fertig, dann hat man einen kleinen Tribosystemwürfel und kann sich über die Eingangs- und Ausgangsgrößen Gedanken machen.
Eingangsgrößen – welche Art der Aktorik bringt die Bewegung ins Spiel, welche Leistungsdaten hat diese, wird das System durch eine bestimmte Atmosphäre beeinflusst und gegen welche Lasten arbeitet es, also was sind meine Normalkraftvektoren und welche Methoden der Lastaufbringung kommen in Frage?
Ausgangsgrößen – wie äußern sich Reibung und Verschleiß im System mutmaßlich, welche Sensorik ist zielführend für die bestmögliche Beschreibung meines Systems? Wie nah muss ich an meinen Tribosystemwürfel dran, um überhaupt aussagekräftige Information aus dem System zu ziehen und welche Verlustgrößen sind zu erwarten?
Man fügt also zum Tribosystemwürfel den Aktorik und Sensorik Würfel und gegebenenfalls haust man das alles in den Prüfstandwürfel ein (Atmosphärekammer bei Bedarf versteht sich).
Aus rein wissenschaftlicher Sicht ist hier das Gros geleistet, Tribosystem verstanden, Aktorik und Sensorik optimiert, Veröffentlichung eigentlich schon geschrieben. Aus Sicht des Prüfstandsbauers fängt jetzt die Schwierigkeit an – wie kann ich diese Elemente zusammenführen, ohne dass meine Prüfung zu kompromissbehaftet wird? Benötige ich zu viele Lagerungen zur Entkopplung meines rotierenden Systems so messe ich irgendwann mehr Stütz- als Prüflager. Muss ich meinen Tribosystemwürfel abkapseln so ist meine Temperaturmessung möglicherweise zu weit weg von der Reibstelle und ich verliere zu viel wichtige Systeminformation. Es wird also nach einem Bindeglied gesucht.
Mit ausreichend Erfahrung kennt man irgendwann die Standardsysteme gut genug, sodass man für vieles go-to Lösungen oder zumindest Ansätze entwickelt hat, die sich einfach übertragen lassen.
Nicht so für eine Scharnierprüfung für die wir vor geraumer Zeit einen Prüfstand entwickelten. Hier war klar, wie das System funktioniert – ein normalkraftbelasteter Drehniet, eine klar definierte Schwenkbewegung. Wir wussten, dass im Versuch Verschleiß zu erwarten wäre, dass Reibwärme entstehen würde und dass wir im Idealfall das Reibmoment genau auf den Verstellwinkel zurückführen wollen würden. Es war klar, dass es hier kein Normteil geben würde, welches alle Anforderungen erfüllt, also machten wir uns mit dem 3D-Drucker im Gepäck auf, Geometrien zu testen, bis wir uns dem SpezialSchäkel näherten und mit ihm alle unsere Probleme lösen konnten. Der SpezialSchäkel hält nicht nur unser Tribosystem, er ist auch Angriffspunkt für unsere Normalkraft und Temperaturmessung. Klar definierte Flächen ermöglichen zusätzlich optische Wegmessungen für die Schwenkwinkel und Verschleißmessung. Ohne gäbe es die Prüfung in der Form wie sie heute existiert nicht – ein gutes Beispiel dafür, dass im Maschinenbau einzelne Komponenten entscheidend sein können.
Zum Thema Fertigung – wir haben uns schlussendlich dazu entschlossen unseren Schäkel SLM zu drucken. Eine traditionell gefertigte Variante wäre ebenfalls möglich gewesen, beides hat Vor- und Nachteile:
Die traditionell gefertigte Variante ist mehrteilig und bringt durch den Ein- und Ausbau bei jedem Versuch Varianz und Fehlerpotenzial in die Versuchsreihe ein. Die gedruckte Variante muss nach Fertigung aufwändig nachbearbeitet werden, um am Ende den hohen Genauigkeitsanforderungen zu genügen. Dafür ist es ein Teil, was einfach funktioniert.
Kostentechnisch nehmen sich die beiden bei Stückzahl = 1 unterm Strich nichts, ein klarer Vorteil vom 3D-Druck ist aber, dass man Komponenten genau so hin konstruieren kann, wie man sie braucht, ohne zu viel Zeit mit Machbarkeit zu verbringen – da kann man kreativ werden und findet auch mal einfacher die Schlüsselkomponente für seinen Prüfstand.